| |
Iniezione
Nate per correre
Di Andrea Comini
Imbiellaggi su una pressa ad alta velocità Billion Hercule Plus
Ridurre gli spessori dei prodotti è un imperativo dettato da
considerazioni economiche, è vero, ma anche di mercato: se un bicchiere da bibite pesa
pochissimo, vuol dire che si è risparmiato sul materiale e quindi i margini di ricavo
aumentano; se un cellulare neanche sai di averlo, tanto è leggero, aumentano invece le
probabilità che il consumatore lo scelga proprio per questo. E in entrambi i
casi, al restringersi del tempo di ciclo si accompagna lavvicinarsi del sospirato
ammortamento del costo macchina.
Bicchieri e cellulari, agli antipodi sotto diversi aspetti, sono due
esempi applicativi tra i tanti, ma servono a capire perché, da qualche tempo, diversi
costruttori di presse a iniezione abbiano trasformato parte dei propri stabilimenti in
succursali delle scuderie di Formula 1, perennemente alla ricerca di soluzioni che
permettano di tagliare di qualche centesimo di secondo un tempo di risposta,
un movimento o una frenata. I tempi diniezione, nelle applicazioni
hi-speed, si calcolano con sofisticati cronometri che rilevano anche i
millesimi, giacché in certi casi la differenza è davvero tutta lì. Le viti, su queste
presse nate per correre, girano vorticosamente e segnano accelerazioni
da zero a 100 degne di propulsori a 12 cavalli, per restare in ambito
motoristico.
Difficile riuscirci? No, se la scelta di materiali, componenti ed
elettronica è allaltezza e se il know-how della velocità ha solide radici nel
reparto progettazione.
Potenziate, robuste e redditizie
Per applicazioni di stampaggio ad alta velocità, MIR ha sviluppato soluzioni su misura
elaborando i componenti delle macchine standard della serie RMP,
costituita da presse con chiusura a ginocchiera.
Una superiore velocità di stampaggio implica infatti lutilizzo
di materiali maggiormente resistenti allusura per la fabbricazione dei componenti
nonché il potenziamento di tutte le funzioni della pressa, in modo da abbreviare al
massimo i tempi di esecuzione di ciascuna fase del ciclo, sovrapponendo i movimenti
macchina ove possibile.
Ovviamente, le elaborazioni più rilevanti vengono applicate dai
tecnici MIR alle sezioni produttive della pressa, gruppo iniezione e gruppo chiusura, e
alle relative attivazioni idrauliche ed elettriche, ma anche i sistemi di estrazione e di
controllo macchina devono essere ripensati per garantire prestazioni eccezionali in
termini di tempistica e precisione.
Il cilindro di plastificazione, quindi, risulta di
solito più lungo sulle macchine MIR per stampaggio ad alta velocità, perché la
lavorazione del materiale viene eseguita in modo tale da offrire una plastificazione e una
omogeneizzazione superiori; questo grazie a viti, anchesse più lunghe, che ruotano
fino a 600 giri/min (circa il doppio rispetto alla velocità vite raggiunta in diverse
applicazioni standard); viti dotate di speciali sezioni di miscelazione e lavorazione, in
grado di fondere e spingere il polimero verso lugello diniezione in tempi
drasticamente abbreviati rispetto alle presse di serie.
Le pompe idrauliche normalmente responsabili
dellesecuzione della procedura di iniezione sono dotate, sulle macchine per alta
velocità, di motori più potenti, mentre appositi accumulatori oleopneumatici apportano
unulteriore spinta alla fase di iniezione, coordinata con la massima
precisione da una servovalvola Moog, permettendo lesecuzione in pochi centesimi di
secondo, con una pressione superiore a quella convenzionale. La necessaria velocità di
risposta del ciclo di chiusura/apertura è garantita da un sistema idraulico ad alta
efficienza e dallutilizzo di valvole proporzionali, impiegate anche nel sistema di
estrazione.
Il risultato è un ciclo di stampaggio decisamente
compresso: iniezione rapida, immediato raffreddamento del materiale
nelle cavità (grazie a stampi dotati di refrigerazione ad alta efficienza), inizio
apertura e contemporanea espulsione dei pezzi (spesso supportata da getto daria).
Considerati i tempi estremamente ridotti di raffreddamento dei pezzi nello stampo, la
macchina è in grado di caricare la nuova stampata sovrapponendo tale funzione alle fasi
di apertura e chiusura dello stampo.
In questo modo, un normale ciclo di stampaggio di prodotti
tipicamente hi-speed quali i bicchieri usa-e-getta in PS cristallo da
0,4 litri (con spessore di parete pari a 0,4 mm circa), che richiede 5-6 secondi con
macchine standard, viene ridotto a meno della metà (2-2,5 secondi).
Ma se fossero disponibili stampi con sistemi di raffreddamento dei pezzi ancora più
efficaci, le presse MIR ad alta velocità potrebbero scendere senza difficoltà al di
sotto dei 2 secondi di ciclo completo per prodotti di questo genere.
Il limite attuale, spiega il costruttore, è infatti determinato dal raffreddamento del
polimero nella cavità di stampaggio e non dalle rapidità di esecuzione delle macchine,
almeno per quanto riguarda le applicazione a parete sottile, che rappresentano la
stragrande maggioranza delle produzioni eseguite mediante tecniche di stampaggio ad alta
velocità.
Il potenziamento delle presse, come è facile intuire, non riguarda
però soltanto la velocità delle operazioni ma anche la qualità dei componenti;
in caso contrario, lavorando a ritmi così frenetici il logoramento delle parti meccaniche
e delle superfici in contatto con i materiali imporrebbe manutenzioni talmente frequenti
da pregiudicare la redditività della produzione. Ecco quindi ladozione, da parte di
MIR, di componenti dotati di elevata resistenza allusura, sia meccanica sia di
contatto.
I cilindri di plastificazione, ad esempio, sono di tipo bimetallico, mentre le viti
presentano riporti al carburo lungo le filettature, per garantire la necessaria resistenza
allo stress meccanico e allazione spesso abrasiva del polimero in lavorazione. La
grande robustezza dei piani e di tutti gli organi in movimento è altrettanto essenziale
ai fini della lunga durata in servizio della pressa, per cui MIR ha optato per acciai
della massima qualità e per tecniche di fusione capaci di garantire la più alta coesione
del metallo.
Anche i sistemi di estrazione pezzi sono stati
necessariamente adeguati alle stringenti tempistiche di queste applicazioni. Un esempio
tra i tanti riguarda lo stampaggio di posateria, per il quale si è provveduto a
interfacciare il controllo pressa con un piccolo manipolatore che penetra
tra i semistampi nel brevissimo intervallo di apertura (1,5 secondi circa), preleva i
pezzi dalle cavità e li deposita esternamente per ritornare subito a prelevare la
successiva stampata.
Per quanto riguarda il controllo elettronico della
macchina, il costruttore ha ottimizzato e potenziato il software di gestione normalmente
impiegato sulle presse standard, ottenendo anche sulle versioni ad alta velocità
quellaffidabilità e quella precisione che sono tra i punti di forza della gamma
MIR.
Dal punto di vista dei costi, infine, le modifiche
applicate alle RMP di serie non incidono in modo particolarmente significativo per
lacquirente: le versioni hi-speed (disponibili con forze di chiusura da
25 a 450 ton) garantiscono infatti un aumento di produzione che può arrivare al 60% su
base oraria, un margine sufficientemente ampio per conseguire un rapido ammortamento
dellinvestimento.
Tappi e chiusure a raffica
Specializzata già da alcuni anni nella progettazione e costruzione
di macchine a tavola rotante per stampaggio a compressione, operanti ad
alta velocità per la produzione di capsule ed altri oggetti in plastica, la Sacmi sta investendo molte risorse nello
sviluppo di questa tecnologia. Il risultato immediato è un ampliamento della gamma degli
oggetti fabbricabili con materiali sempre nuovi.
Sacmi può contare su oltre 50 anni di esperienza nel settore delle
chiusure per bevande e su più di 500 addetti nella Divisione Beverage & Packaging,
per offrire alla sua clientela un servizio globale unico sul mercato: dallo sviluppo del
progetto allassistenza tecnologica sul prodotto finale.
Con un laboratorio tecnologico allavanguardia, che lavora in
stretto contatto con i principali fornitori di materie plastiche, lazienda di Imola
può offrire tutta lassistenza richiesta, dalla selezione e prova delle materie
prime alla verifica della funzionalità del prodotto finito. Il successo di questa
tipologia di impianti è testimoniata dal notevole numero di macchine installate in
tutto il mondo.
Laccennato ampliamento della gamma di macchine CCM (Continuous
Compression Molding) della Sacmi presenta tre nuove soluzioni:
CCM 010 (24 cavità) che sostituisce il precedente
modello identificato dalla medesima sigla ed è nata per rispondere alla crescente
richiesta di alcuni mercati, in particolare quello americano, di capsule di grandi
dimensioni per lindustria alimentare e può giungere a stampare il formato con
diametro 63.
CCM 002 (64 cavità), studiata per i massimi
volumi produttivi (tipici ad esempio del settore soft-drink) con conseguenti ampie
economie di scala; la macchina è in grado, dal punto di vista meccanico, di produrre
oltre 1.200 capsule/min.
CCM01, nuova macchina sulla quale è possibile
installare un innovativo sistema di estrazione dagli stampi, definito a
svitamento, che consente di stampare diversi tipi di capsule, destinate al settore
dei detergenti, farmaceutico e alimentare, in precedenza non realizzabili mediante la
tecnica a compressione continua
Un aspetto importante dellapproccio di Sacmi al mercato di
riferimento è la capacità di fornire, insieme alla pressa, anche gli stampi necessari
allapplicazione, costruiti internamente allazienda; unofferta completa,
quindi, non certo comune nel settore dello stampaggio a iniezione, da sempre
contraddistinto precisa Sacmi - da una quasi totale divisione fra costruttori di
presse, produttori di stampi e costruttori di accessori.
Oltre che dalla sede centrale di Imola, Sacmi offre ampie garanzie di
servizio globale grazie agli otto magazzini ricambi sparsi nel mondo e a
un notevole supporto di assistenza tecnica. Tutto ciò si aggiunge sottolinea il
costruttore - ai vantaggi consolidati della tecnologia a compressione, vantaggi fatti di
evidenti e riconosciute riduzioni di costi, maggior qualità dei manufatti e superiore
efficienza e produttività delle macchine.
Le nuove soluzioni tecnologiche e impiantistiche per la produzione di
tappi e chiusure sviluppate da Sacmi indicano secondo la stessa azienda un vantaggio
per la compressione che sembra ormai incolmabile. In uno scenario dove la competizione tra
le multinazionali del largo consumo, e quindi tra i loro fornitori, impone da un lato il
mantenimento di elevati standard qualitativi e dallaltro la riduzione dei costi del
prodotto finito (condizione necessaria per facilitare la crescita dei volumi), anche il
tappo in plastica inizia ad assumere un ruolo importante.
Nel corso degli ultimi anni, infatti, molti produttori specializzati
e grandi industrie del beverage hanno affidato a Sacmi il compito di mantenere
gli eccellenti risultati raggiunti con la tecnologia a compressione, per proiettarli però
verso volumi di produzione ancora maggiori. Il risultato tangibile delle possibilità
offerte dalla tecnologia a compressione si è potuto osservare, ad esempio, in occasione
del Plast di Milano, dove era esposta in funzione la macchina Sacmi
CCM 002, capace di raggiungere i 1200 tappi al minuto, con consumi energetici per
tappo prodotto inferiori rispetto alliniezione e la possibilità di effettuare cambi
di formato e colore in pochi minuti.
Secondo Sacmi, questa macchina ha confermato, forse in maniera
definitiva, che il futuro del tappo in plastica è la compressione, in quanto unica
tecnologia in grado di garantire qualità ed efficienza necessarie a soddisfare
lenorme e sempre crescente domanda di tappi e chiusure in plastica proveniente
dallindustria del largo consumo (in particolare, dal segmento beverage),
che andrà ulteriormente aumentando precisa Sacmi grazie al previsto
ampliamento della domanda da parte dellindustria del latte.
Velocità di serie
Rispondere alle richieste della clientela più esigente, in special
modo quando alla precisione si vuole unire la velocità di esecuzione, è sempre stato un
punto fermo dellattività di Billion,
costruttore francese che si appresta a inaugurare la filiale italiana proprio in questi
mesi. Ed è anche per soddisfare queste esigenze che le macchine della serie Hercule
e della Gamma Media sono fornite di serie di accumulatori per la gestione di tutti i
movimenti e di servodistributori sulle fasi di iniezione, per ottenere la massima
sovrapposizione dei movimenti unitamente alla precisione e alla ripetitività
delliniezione.
Per rispondere alle necessità particolarmente esigenti del settore
dello stampaggio ad alta cadenza, Billion ha sviluppato, nellambito della serie
Hercule, una versione denominata Hercule Plus. Queste macchine sono
disponibili con forza di chiusura da 80 a 320 tonnellate e con diverse
tipologie di gruppi iniezione, con possibilità di scegliere fra due diametri vite.
Le Hercule Plus sono dotate di gruppo chiusura idromeccanico,
costituito da una doppia ginocchiera per i movimenti rapidi del piano mobile e da un
cilindro idraulico che esegue il bloccaggio dello stampo.
Gli accumulatori erogano un potenziale di energia adatto ad assicurare la simultaneità
dei movimenti alla massima velocità. Il ciclo di queste presse è concepito in
maniera tale che la partenza delliniezione sia anticipata rispetto al bloccaggio
dello stampo, per ridurre così il tempo di ciclo.
I particolari che compongono il gruppo chiusura sono stati
ideati in funzione delle grandi sollecitazioni che si sviluppano operando ad alta
velocità: limbiellaggio in acciaio ad alta resistenza meccanica assicura
affidabilità e tenuta nel tempo; la particolare struttura a 4V del piano
mobile è stata prevista con una lunghezza di guida pari a 5 volte il diametro delle
colonne, ottenendo così il perfetto parallelismo col piano fisso durante i suoi
movimenti veloci.
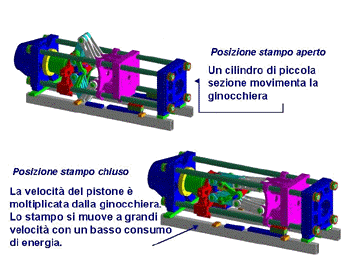
Schema di funzionamento del gruppo chiusura
idromeccanico che equipaggia le presse Billion Hercule Plus
Altro particolare importante è lassenza di
contaminazione dei pezzi stampati, grazie a bronzine autolubrificate per lo
scorrimento del piano mobile e ad uno speciale sistema di supporto del piano stesso che
non prevede lubrificazione.
Il gruppo iniezione delle Hercule Plus prevede,
oltre agli accumulatori, un servodistributore integrato allunità di iniezione e
deputato a pilotare un sistema oleodinamico particolare che controlla landamento dei
dieci passi di grande velocità di iniezione.
La qualità della plastificazione del materiale è
garantita dalla possibilità di scegliere un plastificatore a doppio filetto o
addirittura una vite con rapporto L/D pari 28; se la quantità di materiale è elevata, è
possibile installare due tipi di ugelli idraulici che permettono di eseguire la
plastificazione in contemporanea con le fasi di apertura e chiusura della pressa.
Caratteristica che accomuna tutta la produzione Billion è il sistema
di controllo Dixit, operante via touch screen a colori. Questo sistema, semplice
e intuitivo, con la sua grafica a icone permette una facile e rapida integrazione tra la
macchina e loperatore.
Infine, un accenno alle prestazioni delle Hercule
Plus sottolineate da Billion. Con un modello da 100 tonnellate si ottengono, ad esempio,
due vasetti per giardinaggio spessi 0,6 mm e con peso di 18 grammi in poco più di 2
secondi; con la stessa pressa si ottiene una vaschetta in PP da 0,7 mm di spessore (peso
27 grammi) in 3 secondi.
Con una 140 tonnellate si produce un vasetto di 60 g (spessore 0,7 mm) in 3,5 secondi, con
una capacità di plastificazione pari a 61,2 kg/ora; passando a un modello da 200
tonnellate, è possibile produrre 6 bicchieri in PS (spessore 0,7 mm) con un ciclo
di 4 secondi
Diversi modelli da 320 tonnellate vengono utilizzati da anni per
stampare 24 ore su 24 i tappi da 2,2 grammi in HDPE su stampi da 48 impronte, con cicli di
5,8 secondi; con la stessa pressa vengono inoltre prodotti secchi per vernice da 11 litri
in 9 secondi, raggiungendo un ritmo di plastificazione pari a 118 kg/ora.
continua
>>
|