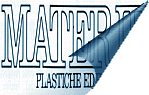
|
Materie Plastiche
ed Elastomeri
Rivista tecnica
|
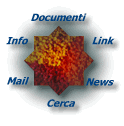
|
Fondata nel 1935
|
Una Pubblicazione:
O.VE.S.T. Srl
Via S. D'orsenigo, 22
20135 Milano
E-mail
redazione
redampe@ovest.it
Direttore
responsabile
Ugo Carutti
Direttore
editoriale Webmaster
Carlo Latorre
Ovest © Tutti i
diritti riservati
|
|
|
|
|
|
|
|
|
|
 |
| |
Report
Risparmiare con la multi-iniezione
Panoramica
dellofferta di presse per lo stampaggio multicolore e multimateriale
Di Giovanni Baucia
Se fino alla fine degli anni 70 parlando di stampaggio ad iniezione era sufficiente
fare distinzione fra lo stampaggio di termoplastici e di termoindurenti, oggi il panorama
tecnologico è più ampio, comprendendo tecniche quali lo stampaggio ad intrusione,
liniezione-compressione, liniezione-transfer, lo stampaggio di materiali
espansi, senza contare le tecnologie ibride. Tra queste, la produzione di manufatti
bicolore/bimateriale ha assunto una posizione di primo piano in quanto consente di
eliminare alcune fasi di lavorazione manuale (come la saldatura o la verniciatura),
offrendo manufatti di buona qualità prestazionale ed estetica. Non solo: lo stampaggio
multi-iniezione ha contribuito allo sviluppo di nuovi materiali plastici e ha aperto nuove
frontiere applicative, soprattutto sul fronte del design.
Lo stampaggio multicolore/multimateriale ha potuto diffondersi in modo rapido e capillare
anche grazie ai progressi messi in atto dai costruttori di stampi, attraverso lo sviluppo
di complessi movimenti degli stampi (a cominciare dalla rotazione) e cicli speciali, che
lasciano - per esempio il necessario spazio nelle cavità per lintroduzione
del secondo materiale. Anche lautomazione di processo è stata daiuto,
soprattutto con lo sviluppo di robot e manipolatori che agevolano la traslazione della
stampata tra le successive iniezioni.
Nelle pagine seguenti analizziamo lofferta di sistemi multi-iniezione costruiti da
aziende italiane ed estere, una panoramica che seppur non esaustiva, mette in luce le
diversità (e talvolta le somiglianze) delle diverse proposte. Ma lo stato dellarte
è solo un aspetto di questa tecnologia, in costante evoluzione: gli esperti del settore
sono infatti concordi nellaffermare che questa tecnologia è ben lontana
dallaver esaurito tutte le possibilità applicative e le potenzialità di mercato.
MIR: la flessibilità è di casa
Iniziamo la nostra panoramica con la bresciana MIR, che propone una completa gamma di
soluzioni nel campo dello stampaggio ad iniezione di termoplastici, termoindurenti ed
elastomeri. Per quanto concerne la multi-iniezione, lazienda è in grado di fornire
tecnologie di costampaggio e coiniezione, che si caratterizzano per la possibilità di
eliminare le post-lavorazioni in molti processi. È il caso, per esempio, del costampaggio
di elastomeri e tecnopolimeri, che ha permesso di produrre in ciclo automatico elementi di
tenuta o di insonorizzazione.
Franco Inverardi ci spiega che MIR progetta le presse per il costampaggio secondo due
sistemi: il primo, più diffuso, è basato su una pressa bi-iniezione equipaggiata con una
tavola rotante fissata sul piano mobile: la configurazione prevede due semistampi bloccati
sul piano fisso e due semistampi bloccati sulla tavola rotante. La sequenza del ciclo è
così articolata: chiusura stampo, iniezione primo materiale, apertura stampo, rotazione
tavola, chiusura stampo, iniezione secondo materiale, apertura stampo, estrazione.
Nel secondo caso la tecnologia è basata sulla costruzione degli stampi. Si utilizza
sempre una pressa bi-iniezione, però senza tavola rotante. Lo stampo dispone di movimenti
meccanici interni in grado di creare, nei tempi dovuti, degli spazi in cui iniettare il
secondo materiale; questo sistema riduce il costo degli stampi - che possono essere quelli
esistenti - con investimenti iniziali contenuti, oltre ad offrire riduzioni dei tempi di
ciclo.
La coiniezione consiste nelliniettare due diversi polimeri allinterno della
cavità dello stampo tramite un solo canale di iniezione, con presse dotate di doppia
iniezione traslabile. Le prime applicazioni sono state la produzione di manufatti con
allinterno materiale riciclato ed allesterno polimero vergine. La sequenza del
ciclo è la seguente: si inietta dapprima il materiale che dovrà fungere da rivestimento
e, successivamente - in una seconda fase - quello che costituisce lanima. In
funzione del tipo di materiale e delle relative temperature di trasformazione
liniezione può avvenire mediante due gruppi separati a canali caldi - i materiali
rimangono così separati fino allingresso della cavità dello stampo oppure,
nel caso di plastificazioni con temperature simili, si può impiegare una testata che
unisce i due gruppi in modo da consentire liniezione tramite un singolo ugello.
Recentemente la MIR ha messo sul mercato una serie di presse Multi-Iniezione, flessibili e
versatili, con forza di chiusura compresa tra 100 e 2.000 t. Queste macchine sono in grado
di rispondere ad ogni esigenza di costampaggio, ma funzionano altrettanto bene nello
stampaggio tradizionale. Infatti, mediante particolari movimenti della cavità dello
stampo è possibile costampare due materiali diversi senza la tavola rotante con vantaggi
in termini di tempi di ciclo e, quindi, dei costi.
Le presse Multi-Iniezione sono equipaggiate con due iniettori che possono essere
alimentati con due materiali diversi, nel caso di coiniezione, oppure è possibile
posizionare un solo iniettore al centro della macchina per un utilizzo tradizionale. Il
movimento idraulico allinterno dello stampo - che è dotato di un numero superiore
di cavità - consente anche di utilizzare stampi di ingombro ridotto.
Per grandi manufatti ci sono le rotative
La Presma di Gornate Olona, Varese, vanta il primato della costruzione in Italia di
presse bicomponenti per la produzione di manufatti con nucleo espanso o semiespanso e
rivestimento esterno in materiale compatto, presentate allinizio degli anni
settanta. Attualmente questa società, come già illustrato in un altro articolo in questo
stesso fascicolo, costruisce presse rotative adatte per lo stampaggio bicomponente di
manufatti di grandi dimensioni e peso ridotto, caratterizzate da tempi di ciclo ridotti e
perciò da unelevata produttività. Propone inoltre presse ad iniezione orizzontali
o verticali per lo stampaggio multicolore, multimateriale o con inserti, con forze di
chiusura da 50 a 450 t, costruite su misura secondo le esigenze applicative dello
stampatore. Nel caso per esempio di produzione di manici per cacciaviti in tre materiali
con diversi tempi di raffreddamento, Presma ha recentemente fornito unisola di
lavoro con tre presse modulari (gruppo di chiusura verticale ed iniezione orizzontale)
asservite da due robot antropomorfi per la traslazione delle stampate da una macchina
allaltra.
Engel Combimelt: di speciale solo il nome
Engel, che ha iniziato circa 40 anni fa a costruire presse multicolore/multimateriale,
ha raggruppato tutte le attività riguardanti questa tecnologia nella denominazione
Combimelt. Va sottolineato che le presse Combimelt non sono macchine speciali, piuttosto
sono presse standard attrezzate con gruppi modulari adattati alle specifiche esigenze di
stampaggio. E da rilevare inoltre che la particolare costruzione senza colonne delle
presse ben si addice a questa tecnologia poiché consente lo sfruttamento ottimale dei
piani e favorisce laccessibilità agli stampi, lautomazione del processo e la
flessibilità di utilizzo.
Come già specificato in un altro articolo della Rivista, la tecnologia Combimelt
comprende tutte le varianti di processo per liniezione di compositi di
termoplastici, elastomeri e termoindurenti, tra cui il processo di addizione (iniezione
affiancata), overmolding (iniezione sovrapposta), inmolding (iniezione interna),
costampaggio-sandwich ecc.
Grazie alla modularità dei sistemi e delle macchine, Engel è in grado di offrire un
ampio programma di presse Combimelt attrezzate con stampi e robot di propria costruzione,
con relativi controlli computerizzati. Partendo dal classico sistema a tavola rotante,
Engel ha sviluppato nuove varianti tecnologiche: piastre di posizionamento Index,
spostamento o trasferimento dei pezzi prestampati mediante manipolatori, tassello mobile
con coiniezione (produzione di compositi sandwich multistrato) ed altro ancora.
Ergotech anche per la multi-iniezione
Ergotech Multi è il nome del programma Demag che ha ispirato la concezione costruttiva
della serie di presse ad iniezione multicomponente/multicolore, proposte con forza di
chiusura da 500 fino a 2.000 kN. Ingo Meyer, della Demag Ergotech Italia, spiega che la
serie multi è fondata sulla ben collaudata serie di macchine modulari Ergotech, costruite
in Germania nei due stabilimenti di Schwaig e Wiehe e realizzate, dal 1992 a oggi, in
oltre 10mila esemplari.
Alla costruzione base vengono aggiunti, secondo limpiego specifico, unità di
iniezione supplementari in quattro varianti:
1) In posizione verticale, con iniezione nella giunzione stampo od in un canale caldo;
questa posizione risulta particolarmente vantaggiosa per le presse piccole, con forza di
chiusura sino a 1.100 kN, poiché combina alla compattezza i vantaggi di un iniettore
verticale; in particolare, lascia spazio libero sopra larea di montaggio stampi, con
benefici per il cambio stampi e per linserimento di manipolatori.
2) In configurazione "R", con la seconda unità iniezione posta trasversalmente
sopra la prima. Questa soluzione è caratterizzata da unelevata flessibilità; è
possibile, infatti, iniettare e dosare in contemporanea od in sequenza, alimentare il fuso
in modo semplice (per esempio, secondo il processo "core back", con movimenti
interni nello stampo) nella prossimità della cavità, senza canali caldi e con materozza
minima. Questa posizione offre anche minimi ingombri e facilita il montaggio e lo
smontaggio dello stampo.
3) In versione "L", ove liniezione avviene lateralmente dal retro
macchina, nella giunzione stampo, oppure in un canale caldo. Questa configurazione offre
una superiore stabilità, grazie al supporto separato per lulteriore iniettore.
4) In configurazione "P", con iniettori paralleli; come per la R, ciò consente
liniezione multi-componente con ingombri minimi. Questa soluzione è particolarmente
indicata per le Ergotech di maggiori dimensioni, in caso di grandi stampate, con iniettori
di pari grandezza e con tavola rotante; un altro vantaggio è il cambio rapido del
cilindro.
Le presse Ergotech multi sono equipaggiate con comando computerizzato NC4, lo stesso
montato sulle macchine standard; il sistema è stato però ampliato con laggiunta di
alcune funzioni relative alla tecnologia multicomponente. È possibile completare la
pressa con robot per linserimento/estrazione e il trasferimento del pezzo
pre-iniettato nella stazione successiva, sino alla composizione di isole produttive
complete, come viste in funzione in diverse esposizioni fieristiche.
Meyer ci ha illustrato una novità che dimostra come la tecnologia del multicomponente non
sia affatto matura. Demag Ergotech, in collaborazione con la società danese Gram
Technology, ha messo a punto una nuova tecnologia brevettata, basata su uno stampo a
piani, con due piani di separazione paralleli nei quali sono disposte le cavità per la
prima stampata e per il pezzo finito; il trasferimento avviene mediante rotazione di una
piastra centrale. Questo sistema permette di raddoppiare il numero delle cavità per
dimensioni identiche degli stampi ed abbrevia il tempo di ciclo; in particolare, è
indicato per la produzione di tappi di chiusura. Una pressa Ergotech 50-12 h/80 V multi
con forza di chiusura di 500 kN, attrezzata con uno stampo a piani, stampava con
lunità verticale il supporto di un tappo in PE-LD, sovrastampato mediante unità
orizzontale con una chiusura filettata in PP copolimero.
È interessante rilevare, infine, come la serie Ergotech multi si presti a svariate
combinazioni per lo stampaggio a tre o più componenti. Possono essere combinati, per
esempio, ununità di iniezione orizzontale, una verticale ed una in posizione
laterale; due unità orizzontali ed una in posizione laterale; due iniettori orizzontali
ed uno in posizione verticale.
Netstal: con le Synergy la multi-iniezione non è un problema
Secondo i tecnici Netstal lo stampaggio a due componenti/due colori è una tecnologia
che offre ancora nuove potenzialità di mercato, poiché gli stampatori si trovano a dover
affrontare esigenze sempre più elevate in termini di qualità del manufatto, tempi di
ciclo, funzionalità e design. Esigenze sentite soprattutto nella produzione di pezzi
strutturali per lindustria automobilistica, il medicale ed i beni di consumo.
La società svizzera propone 11 modelli di presse Synergy 2 C (con forza di chiusura da
600 a 4.200 kN) che, attrezzate con due gruppi diniezione, operano secondo tre
tecnologie: overmolding in tre varianti, bi-iniezione e coiniezione. Per tutte queste
tecnologie valgono in generale le seguenti considerazioni: è possibile scegliere il
gruppo per la prima iniezione; si può operare con diverse modalità diniezione in
quanto i gruppi possono stampare contemporaneamente, ad intervalli nel tempo oppure in
sequenza; vi è un adattamento flessibile allo stampo; programmazione e servizio semplici;
elevata costanza del processo dei due gruppi in virtù della doppia regolazione Sycap in
circuito chiuso; passaggio senza problemi alla produzione monocomponente.
Vi è poi la bi-iniezione, vale a dire liniezione, durante lo stesso ciclo, di due
materiali nella medesima cavità; essa viene adottata quando sono previsti requisiti
severi per le superfici, che devono essere successivamente verniciate o marcate.
Infine, la coiniezione è impiegata quando, per motivi di costi e funzionalità, il nucleo
e la pellicola esterna devono essere prodotti in materiali diversi. Per esempio, il nucleo
in riciclato o materiale con caratteristiche barriera e la pellicola esterna in materiale
vergine. In questo processo i due materiali vengono iniettati uno dopo laltro nella
cavità mediante un unico ugello. Dapprima il materiale esterno, poi il nucleo, in modo
tale che il primo materiale venga sospinto dal secondo verso la parete della cavità.
Va notato che nello stampaggio di manufatti a pareti sottili o con funzione barriera è
assolutamente indispensabile che i materiali non si mescolino tra loro; in questo caso è
di ausilio la regolazione Sycap che consente di programmare e regolare automaticamente la
forza di chiusura. Il sistema idraulico delle Synergy 2 C, sorretto da accumulatori, offre
movimenti paralleli indipendenti, riduzione del tempo di ciclo e risparmi energetici
grazie al comando a doppia pompa.
OIMA Stratos BX
Massimo Costa, della OIMA, tiene a precisare che tutte le versioni di presse ad
iniezione Stratos della società trevigiana sono realizzate anche in versione Stratos BX
per stampaggio ad iniezione multicolore o bi-materiale. La tecnologia adottata ha portato
alla costruzione di presse con la stessa unità di chiusura delle presse standard
(ginocchiera o tipo Hydroblock), con forza da 100 a 2.200 t. La maggior parte delle
applicazioni di questo settore riguarda però la gamma di forze da 150 a 700 t.
Ciò che cambia, ovviamente, è il gruppo di iniezione, composto da due o tre gruppi di
plastificazione separati; la posizione ed il numero dipende dallutilizzo cui la
macchina è destinata, dalla tipologia del prodotto e dalla costruzione dello stampo.
Il sistema di iniezione di una pressa serie BX - nota Costa - prevede un gruppo di
plastificazione primario ed uno secondario, ma può essere installato anche un terzo
gruppo. Il diametro e le dimensioni dei primi due gruppi possono essere scelti fra quelli
del programma costruttivo, mentre il terzo gruppo orizzontale - posizionato lateralmente
nella parte opposta alloperatore, in direzione ortogonale allasse della
macchina - viene limitato allEuromap 420. È possibile applicare al gruppo chiusura
una tavola rotante sul piano mobile, per la rotazione stampo di 180°; tale particolarità
è richiesta nel caso si debba realizzare uno stampaggio multicolore o multimateriale e lo
stampo non sia dotato di altri meccanismi idonei allo scopo.
Le applicazioni di queste macchine sono diverse: in particolare è possibile effettuare
una iniezione monomateriale con il gruppo principale e secondario, anche
contemporaneamente; viene per lo più adottata con questi due gruppi una iniezione
bimateriale o bicolore in sequenza o contemporaneamente, con o senza tavola rotante.
E possibile anche liniezione bicolore o bimateriale con il gruppo principale e
quello ortogonale, come pure una iniezione multi-materiale utilizzando tutti i tre gruppi,
in sequenza o contemporaneamente, anche in questo caso con o senza tavola rotante.
Anche la versione Stratos BX con i gruppi principale e secondario posizionati affiancati e
paralleli prevede lutilizzo della testa di coiniezione. Unaltra interessante
configurazione prevede il gruppo principale ed il gruppo ausiliario orizzontale; con il
primo gruppo si esegue uniniezione monomateriale, mentre con gli altri due
uniniezione bimateriale o bicolore, in sequenza o contemporaneamente. E
possibile ottenere le medesime caratteristiche anche con il gruppo principale e il gruppo
ausiliare disposto in posizione verticale.
Per lo stampaggio multi-iniezione OIMA propone anche le presse verticali Lotus BX per
costampaggio o bicolore e stampi traslanti, come pure la serie TX per bicolore o
bimateriale; queste macchine, originariamente progettate per il settore calzaturiero,
vengono sempre più spesso impiegate anche per lo stampaggio di particolari tecnici.
Krauss Maffei Multinject
Krauss Maffei Kunststofftechnik propone per lo stampaggio ad iniezione di articoli
bicolore e bicomponenti la serie Multinject. Claudio Braga, della filiale italiana, ci fa
presente che i componenti principali delle macchine fanno parte del programma standard. La
gamma offerta dal costruttore tedesco si basa cioè su macchine ad iniezione della Serie C
e MC con forza di chiusura da 650 kN a 27.000 kN. In particolare, le presse per
multi-iniezione nella fascia da KM 65 CZ a KM 650 CZ sono basate sulla gamma della serie
C, mentre fino alla KM 150 CZ compresa, il secondo gruppo di iniezione è posizionato in
verticale.
In funzione delle necessità specifiche, il sistema modulare offre numerose possibilità
riguardo i gruppi supplementari e permette la combinazione di fino a quattro gruppi
diniezione, anche se la configurazione più diffusa prevede il secondo gruppo di
iniezione posizionato in verticale.
Il compatto sistema di chiusura idraulico sulle quattro colonne garantisce una
distribuzione uniforme della forza di chiusura fino al massimo del tonnellaggio della
macchina. Lo sviluppo della forza di chiusura avviene mediante quattro pistoni collegati
fra loro e fissati al piano fisso della pressa. Questa configurazione costruttiva, unita
allampio passaggio tra le colonne della Serie C, consente di adottare anche stampi
molto ingombranti, come spesso richiesto nello stampaggio multi-componente.
Per facilitare il cambio stampi dallalto, il gruppo diniezione verticale -
posto su apposite guide di scorrimento con cuscinetti a sfera - può essere traslato con
una semplice operazione oltre il piano fisso della macchina. Possono essere applicate
eventuali tavole rotanti e unità indipendenti direttamente sul piano mobile della pressa.
Per quanto concerne leventuale impiego di manipolatori per lestrazione dei
pezzi, questi possono essere fissati sul lato posteriore del piano fisso della macchina,
mentre la corsa del manipolatore avviene lungo lasse longitudinale. Lo scarico dei
manufatti è affidato a nastri trasportatori posizionati in testa alla macchina dietro al
gruppo di chiusura, oppure direttamente allinterno delle protezioni di sicurezza.
Sui modelli da KM 175 CZ fino a KM 650 CZ non è consigliato il montaggio di un gruppo
diniezione verticale sopra il piano fisso. In questo caso il gruppo diniezione
supplementare è montato in posizione inclinata sopra il gruppo principale. Entrambi i
gruppi lavorano in modo indipendente, per quanto concerne sia le funzioni del ciclo sia
larretramento del carro iniezione. Lo stampo è accessibile da tutti i tre lati ed
eventuali manipolatori possono essere montati sul piano fisso della macchina. Anche per
quanto concerne le macchine per multicomponenti della Serie MC il gruppo iniezione è
inclinato sopra lunità di iniezione principale. In ogni caso, per macchine di
tonnellaggio oltre 8.000 kN di forza di chiusura sono possibili anche configurazioni
particolari secondo le specifiche esigenze del trasformatore.
Le presse Multinject, come tutte le macchine Krauss Maffei, sono equipaggiate con il nuovo
sistema di controllo multiprocessore MC4, che includono anche il comando dei gruppi di
iniezione supplementari ed eventuali cicli speciali. Un sistema operativo multitasking a
32 bit ad alta velocità di elaborazione garantisce una veloce visualizzazione dei valori
reali, grafici ecc.
BMB crede alla versatilità
La BMB di Brescia costruisce presse ad iniezione dedicate allo stampaggio multicolore e
multimateriale con forza di chiusura compresa tra 1.000 a 3.800 kN. La caratteristica
principale del programma BMB è la versatilità che si concretizza in un gran numero di
versioni disponibili, che secondo le necessità possono essere dotate di tavola rotante
con due iniettori paralleli o con iniettore laterale, oppure prive di tavola rotante con
iniettori paralleli, iniettore verticale o laterale.
Un esempio della versatilità è la possibilità di acquistare singolarmente gli
iniettori, da applicare alle macchine in funzione dello specifico articolo da produrre. In
pratica, gli iniettori ausiliari non sono più una parte integrante della macchina, ma
sono diventati accessori da montare e smontare secondo necessità, così come avviene per
gli stampi.
Nella maggioranza dei casi, le presse dedicate alla multi-iniezione vengono realizzate
dotando una macchina standard di un iniettore supplementare che viene applicato sopra il
piano fisso oppure lateralmente, dal lato opposto alloperatore; questa soluzione,
tra laltro, permette di poter operare anche con uno stampo tradizionale, senza
impiego di un iniettore ausiliario. La soluzione del montaggio delliniettore
laterale permette di attrezzare la macchina con un manipolatore per il prelevamento dei
particolari stampati. Nel caso liniettore venga installato verticalmente sopra il
piano fisso, un dispositivo appropriato facilita lo spostamento per il montaggio dello
stampo.
Le macchine dotate invece di due iniettori paralleli presentano una configurazione
specifica che viene determinata dalla tipologia degli stampi che di volta in volta vengono
montati; vengono inoltre forniti sistemi di regolazione per adattarsi ai diversi interassi
dei due canali diniezione. Integrazione di queste specifiche macchine è senza
dubbio lutilizzo di una tavola rotante applicata sul piano mobile, il cui movimento
è affidato ad un motore elettrico dedicato (assistito da inverter) e controllato da
specifici sensori che garantiscono, anche in condizioni di lavoro gravose, una rotazione
precisa e costante in termini di velocità e precisione del posizionamento (per garantire
una perfetta unione delle due metà stampo).
Il costampaggio e il multicolore presentano una peculiarità comune: in entrambi i casi,
infatti, cè una differenza notevole di peso tra i materiali che compongono il
manufatto. Per questa ragione BMB ha progettato gruppi di iniezione supplementari in base
alle specifiche fornite dal cliente.
Loleodinamica e lelettronica (appositamente realizzati) hanno avuto, in questi
tipi di macchine, unevoluzione tecnologica che permette il controllo indipendente
dei cilindri anche in funzione della diversità di materiale o di grammatura, per
garantire nel tempo qualità ed elevata costanza. Inoltre, liniezione è controllata
in anello chiuso tramite una servovalvola (di serie) al fine di assicurare ripetibilità
dei parametri di processo.
Battenfeld tra i pionieri
Ingrid Bergmann, della Battenfeld, ci ricorda che la sua società presentò circa 25
anni fa un impianto costruito dalla Casa Madre Schlömann-Siemag che operava, utilizzando
la tecnologia a due canali della Ici e la fase simultanea, lo stampaggio di più
componenti di materiale plastico. Questo processo venne adottato inizialmente per la
produzione di manufatti di grande spessore con nucleo espanso e pellicola esterna
compatta, con vantaggi in termini di minor peso, eliminazione dei punti difettosi e
tensioni interne, migliore qualità superficiale. Un esempio sono le grandi carcasse di
televisori, spesse 5-6 mm, realizzate con PS espanso (nucleo) e compatto (esterno).
Ben presto però - rileva Bergmann - questo processo venne impiegato anche per lo
stampaggio di due materiali plastici compatti (con spessori della parete fino a 4 mm),
ottenendo applicazioni innovative: per esempio carcasse schermate, additivando il nucleo o
la pellicola esterna con grafite, fibre di acciaio o di carbonio metallizzate.
Per rispondere alle diverse esigenze, Battenfeld ha messo a punto un ampio programma
costruttivo di presse a più componenti, che corrispondono come gruppo di chiusura alle
presse serie HM, CDC e BK. La differenza consiste nellunità di iniezione,
equipaggiata con due gruppi generalmente disposti parallelamente e della medesima
potenzialità. Ciò che caratterizza la tecnologia Battenfeld è però la testa ad
iniezione brevettata, con due canali, posta fra il gruppo di iniezione e lo stampo. Due
materiali possono essere iniettati nello stampo attraverso due canali concentrici
separati, ognuno con una chiusura indipendente a comando idraulico. Con questo sistema
possono essere prodotti, mediante una fase simultanea precisa e regolabile, manufatti
senza marcature e variazioni di lucentezza.
Liniezione del materiale del nucleo inizia prima che la materia prima per la
pellicola sia completamente iniettata. In questo modo la velocità del fronte di
scorrimento rimane costante e non si verificano picchi di pressione o brusche variazioni.
La tecnologia della testa di iniezione a due ugelli è stata ulteriormente perfezionata.
Tra le innovazioni più recenti vanno segnalati lampliamento dello stampaggio da due
a tre componenti, anche in combinazione con stampaggio assistito da gas e stampaggio ad
intervalli; il sistema a due canali reologicamente ottimizzato in modo da consentire lo
stampaggio anche di materiali termicamente sensibili; rapido lavaggio, in virtù dei corti
canali di collegamento, che semplifica il cambio di materiale.
Arburg punta sulle Allrounder
Arburg ha iniziato la costruzione di presse per bicomponenti nel 1961; oggi, con quasi
quarantanni di esperienza, propone diverse serie di presse progettate secondo
varianti tecnologiche quali lo stampaggio ad iniezione con stampo rotante, ad intervalli,
iniezione sandwich o stampaggio con stampo non rotante.
Illustriamo in particolare le serie maggiormente diffuse, Allrounder C e S, equipaggiate
per lo stampaggio bicomponente mediante speciali gruppi di iniezione ed accessori (unità
di rotazione, unità ad intervalli od anime). Le presse C, con forza di chiusura da 1.000
a 2.000 kN, sono provviste di un gruppo iniezione orizzontale e di uno verticale che, in
alternativa, può essere disposto a "L", in questo caso iniettando
orizzontalmente tra i semistampi.
Interessante è la tecnologia di iniezione ad intervalli, che ha avuto successo nella
produzione di manufatti che richiedono speciali effetti cromatici come pettini, bottoni,
fibbie, accessori per abbigliamento, oggetti regalo ecc. I due componenti vengono
iniettati nelle cavità in modo alternato per mezzo di un apposito ugello fuori stampo,
anteposto alla materozza. Diversamente dal tradizionale stampaggio ad iniezione
bicomponente, con questa tecnologia si ottengono speciali effetti cromatici grazie alla
fusione delle due materie plastiche. In questo caso i colori non risultano ben definiti in
quanto ciò che si vuole ottenere è proprio la loro miscelazione. Per ottenere questo
effetto i due gruppi vengono collegati ad una speciale unità a intervalli,
allinterno della quale si trova lugello di miscelazione. Lunità a
intervalli viene fissata sulla piastra porta-stampo fissa della pressa e, quindi,
anteposta allo stampo. Uno speciale programma del sistema di controllo Selogica determina
la giusta cadenza degli intervalli regola i flussi di colata. Smontando lunità ad
intervalli la macchina può essere utilizzata anche per lo stampaggio ad iniezione di due
componenti.
Nel caso della serie Allrounder S sono state mantenute le caratteristiche base, quali la
struttura modulare, il controllo Selogica e la ridotta superficie di ingombro. Anche in
questo caso è possibile configurare la pressa più idonea per ogni applicazione specifica
assemblando i vari moduli. Tutte le attrezzature periferiche sono integrate nel basamento,
così da ridurre al minimo gli ingombri anche nel caso di macchine per lo stampaggio
bicomponente.
Le Allrounder S sono disponibili, come presse per bicomponenti, con forza di chiusura di
350 e 500 kN. Si possono assemblare diversi gruppi di iniezione orizzontali con grandezza
Euromap da 60, 150 e 350 e verticali da 60 e 150. Il gruppo di chiusura ed i due gruppi di
iniezione sono disposti su un montante macchina prolungato, nel quale è integrato il
complesso idraulico, costituito da due pompe principali servoregolate e da una ulteriore
pompa per il mantenimento della pressione. La piastra portastampo mobile con cilindri
arretrati lascia spazio libero nella zona del gruppo di chiusura per le unità di
rotazione. È da rilevare che il prolungamento di 100 mm delle colonne consente di
installare anche stampi complessi e manipolatori di grandi dimensioni.
La società ha messo sul mercato anche presse dellultima serie C Jubilee con due
unità di iniezione per applicazioni multicomponente; citiamo a tale proposito il modello
520 C Jubilee con forza di chiusura di 2.000 KN e controllo Selogica. Con questa macchina
- in esecuzione a tavola rotante - è stata stampata, per esempio, una carcassa
portaspazzole per lucidatrice. La base, robusta e resistente allurto, è in PP
rinforzato vetro, mentre nella sezione inferiore è stato applicato, sempre per iniezione,
un bordo-guarnizione di PE. Lo stampaggio è stato eseguito dalla Gerdena, che ha
costruito anche lo stampo a due cavità (una per la carcassa e laltra per la
guarnizione). A tale scopo è stato utilizzato anche un manipolatore della Geiger, con
rimozione automatica della materozza, operazione programmata dal controllo Selogica
BM Biraghi Sintesi Twin
BM Biraghi propone la linea di presse Sintesi Twin. Labbinamento del modulo base
standard con i gruppi ad iniezione disposti secondo differenti orientamenti
(perpendicolare, parallelo od obliquo) consente lo stampaggio sia di parti multicolore con
stampo rotante su tavola ed iniezione simultanea dei colori, sia secondo la tecnologia
della movimentazione interna allo stampo ed iniezione sequenziale dei materiali con
sovrastampaggio. Con la stessa serie di macchine sono possibili stampaggi multicomponenti
(combinazione di un termoplastico rigido con TPE) oppure parti con nucleo di materiale
rinforzato e strato superficiale con funzione estetica, od ancora pezzi di grande spessore
con strato interno in materiale rigenerato. Il tutto con controllo totalmente indipendente
delle varie unità di iniezione.
La coiniezione può essere effettuata nellugello di miscelazione della macchina o
direttamente nello stampo. In questultimo caso se lo stampo è più complesso, la
pressa offre una maggiore flessibilità ed è quindi utilizzabile per svariate
applicazioni.
Il più recente modello della serie Sintesi Twin, 680/770/310, è stato recentemente
consegnato alla società inglese Precision Cut Rubber Ltd; si tratta di una pressa con
forza di chiusura di 680 t equipaggiata con stampo traslante sul piano fisso. Dati i
ridotti pesi dei componenti, la macchina è dotata di due gruppi di iniezione (uno
verticale ed uno orizzontale) di piccole dimensioni pur mantenendo inalterati, grazie al
sistema modulare, il basamento del gruppo iniezione e limpianto idraulico di
comando. In questo modo il trasformatore potrà in futuro montare il gruppo di iniezione
della 680 t. Con questa macchina viene stampato, con tecnica sequenziale, un profilato con
tenuta che avvolge il fanale anteriore della Ford Focus.
La società monzese distribuisce in Italia anche le presse Boy, il cui programma comprende
anche una modello per bicolore e bimateriale. Si tratta del modello Boy 30-2C,
equipaggiato con due gruppi iniezione, uno verticale (con sei diversi tipi di vite) e
laltro orizzontale (tre viti). Il gruppo di chiusura è identico a quello montato
sulla versione standard, con forza di chiusura di 306 kN. I cilindri di chiusura sono
integrati nel piano fisso e gli steli agiscono anche come colonne. La costruzione a due
piani minimizza il numero delle parti in movimento riducendo lusura. È possibile
utilizzare, senza alcun problema, anche stampi con cavità asimmetriche.
Altre caratteristiche delle presse Boy sono le due pompe a portata variabile controllate
elettronicamente (che assicurano flessibilità per entrambe le sequenze e per
liniezione parallela) e il controllo a microprocessore Procan CT, con video
"touch screen". Inoltre, i due gruppi iniezione possono essere controllati
indipendentemente consentendo la produzione di manufatti con maggiore precisione e
ripetibilità di ciclo.
|