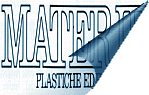
|
Materie Plastiche
ed Elastomeri
Rivista tecnica
|
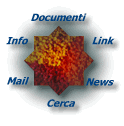
|
Fondata nel 1935
|
Una Pubblicazione:
O.VE.S.T. Srl
Via S. D'orsenigo, 22
20135 Milano
E-mail
redazione
redampe@ovest.it
Direttore
responsabile
Ugo Carutti
Direttore
editoriale Webmaster
Carlo Latorre
Ovest © Tutti i
diritti riservati
|
|
|
|
|
|
|
|
|
|
 |
| |
Attualità'
PVC ancora più competitivo grazie alletano
ECV ha costruito un impianto pilota per la sintesi di CVM direttamente da etano,
una tecnologia che promette il dimezzamento dei costi di produzione del PVC
Di Carlo Latorre
Greenpeace non esulterà per lannuncio dato da EVC sulla messa a punto di un
innovativo processo per la produzione di cloruro di vinile direttamente da etano. La
ragione non è di carattere ambientale, tuttaltro, ma squisitamente politica: la
nuova tecnologia, infatti, promette di produrre PVC con costi ancora più bassi si
parla di circa il 30-50% e come è noto è proprio il buon rapporto
prezzo/prestazioni a decretare il successo di questo polimero.
Per la stessa ragione non esulteranno nemmeno i produttori di polimeri concorrenti,
poliolefine e stirenici soprattutto, mentre benefici sostanziali sono attesi per i
trasformatori, anche se non saranno immediati. Dando per scontato che i risultati
dellimpianto pilota di Wilhelshaven confermino le attese, ci vorranno almeno 10-15
anni perché la tecnologia si diffonda influenzando il livello dei prezzi. " La
sperimentazione nellimpianto pilota si concluderà nel 2001 ha spiegato in un
incontro con la stampa Ettore dellIsola, Chairman di EVC mentre il primo
impianto industriale è previsto per lanno 2003". Quasi certamente la
produzione non avverrà in Europa, in ragione della scarsa disponibilità di etano, mentre
potrebbero candidarsi i paesi nellarea del Golfo Persico, Australia, Messico e, più
vicino a noi, lAlgeria.
Un successo per la ricerca italiana
Il processo è stato sviluppato da Inovyl divisione tecnologica del gruppo EVC
a Porto Marghera e sarà commercializzato in collaborazione con lazienda
statunitense Betchtel. Se da un lato è un riconoscimento per la ricerca italiana, il
fatto che limpianto pilota semi-industriale sia stato costruito in Germania e non
nel nostro paese è sintomatico. La scelta del sito di Wilhelshaven non dipende infatti da
ragioni industriali anzi, il luogo più idoneo sarebbe stato proprio Porto Marghera
ma dallinerzia delle autorità e dalle lungaggini burocratiche. "Abbiamo
richiesto le autorizzazioni in Italia, senza ottenere risposte afferma
dellIsola mentre in Germania sono state sufficienti due settimane per avere
il via libera". Unaltra occasione persa per il nostro paese, che corre il
rischio, almeno per la chimica (ma non solo), di subire una progressiva
de-industrializzazione con conseguente perdita di know-how e opportunità di formazione ad
alto livello.
Come funziona
Con i processi tradizionali, la produzione di cloruro di vinile (CVM) parte da cloro ed
etilene, fatta eccezione per alcuni vecchi impianti che utilizzano ancora acetilene. I due
ingredienti vengono fatti reagire per produrre dicloretano (DCE), in seguito trasformato
mediante cracker in CVM. Il processo produttivo richiede quindi due cracker (uno per
letilene, laltro per il CVM) e due reattori. Sebbene il cloro sia disponibile
in grandi quantità e sia relativamente economico, letilene è invece costoso ed
entra nella produzione di numerose sostanze chimiche quali poliolefine, poliesteri,
polistirene, elastomeri, solventi industriali, detergenti.
Il nuovo processo EVC utilizza cloro ed etano per produrre direttamente CVM, saltando
così il passaggio di cracking delletilene ed evitando la produzione di DCE. Ne
consegue che è sufficiente un solo reattore e nessun cracker, che come è noto è uno dei
componenti più costosi di un impianto. I benefici non si limitano però ad una maggiore
semplificazione del processo: letano, a differenza delletilene, è molto
economico, abbastanza diffuso (il gas naturale può contenerne fino al 14%) e, non ultimo,
ha scarsi utilizzi commerciali. Utilizzando etano al posto delletilene si possono
così ridurre i costi del CVM fino al 50%, sganciandoli dalle fluttuazioni del prezzo del
petrolio e delle altre materie plastiche contenenti etilene. Secondo una stima EVC, il
costo di una tonnellata di CVM, con processo tradizionale, è di 415 dollari se
letilene viene acquistato allesterno, di 380 dollari in presenza di un
impianto integrato con cracker, mentre il nuovo processo dovrebbe consentire di produrre
una tonnellata di CVM con un costo di soli 255 dollari.
Il nuovo processo promette anche una maggiore efficienza. Nellimpianto pilota di
Wilhelmshaven, con capacità di 1.000 t/a, si è rilevata unalta percentuale di
conversione delle materie prime: 100% di cloro, 99% di ossigeno, oltre il 90% di etano.
Superati i limiti delle alte temperature di reazione
EVC non è stata la prima società a porsi lobiettivo di sostituire
letilene nella produzione di cloruro di vinile monomero. In passato sono stati
compiuti diversi tentativi, falliti per problemi quali la scarsa percentuale di
conversione, linstabilità dei catalizzatori o per fenomeni di corrosione del
reattore, spesso dovuti alle alte temperature di reazione. Si è anche provato ad
utilizzare processi non catalitici, rivelatisi però scarsamente economici quando
trasferiti su scala industriale.
Problemi invece risolti da EVC, grazie alla possibilità di operare con temperature
inferiori a 500°C (si parla di 450°C e anche meno), punto critico per ridurre la
corrosione ed aumentare la vita utile del catalizzatore. La ricetta del catalizzatore è,
ovviamente segreta; le uniche informazioni fornite dallazienda sono che si tratta di
un processo a letto fluido con catalizzatore solido. Da rilevare che per la costruzione
dellimpianto non sono richiesti acciai speciali, altamente resistenti alla
corrosione, e si possono utilizzare come feedstock prodotti e sottoprodotti a base di
cloro, anche in questo caso con elevate percentuali di conversione.
Sotto il profilo ambientale, il nuovo processo dovrebbe apportare alcuni vantaggi, grazie
al minor numero di processi intermedi di produzione. Per lo stesso motivo sarà possibile
realizzare impianti più piccoli e meno onerosi sotto il profilo degli investimenti
iniziali e dei consumi energetici.
|