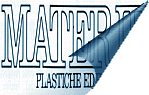
|
Materie Plastiche
ed Elastomeri
Rivista tecnica
|
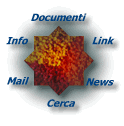
|
Fondata nel 1935
|
Una Pubblicazione:
O.VE.S.T. Srl
Via S. D'orsenigo, 22
20135 Milano
E-mail
redazione
redampe@ovest.it
Direttore
responsabile
Ugo Carutti
Direttore
editoriale Webmaster
Carlo Latorre
Ovest © Tutti i
diritti riservati
|
|
|
|
|
|
|
|
|
|
 |
| |

|
I segreti dellestrusione
|
La tecnologia dellestrusione, nelle sue innumerevoli varianti, caratterizza
da sempre la manifestazione milanese, non fosse altro che per le dimensioni e
limponenza di alcuni impianti esposti in Fiera
a cura della Redazione
Lestrusione è la tecnologia di trasformazione più diffusa, rappresentando circa la
metà degli impianti installati nel nostro paese. Entrano in questo segmento numerose
tipologie di macchine, dai piccoli estrusori fino ai grandi impianti per cast film o film
soffiato, tanto da rendere difficile lidentificazione di linee comuni di sviluppo
tecnologico. Le ultime tendenze, evidenziate anche al Plast, sembrano convergere verso
perfezionamenti nelle tecnologie di coestrusione, lutilizzo di avanzati controlli
per lautomazione di processo e lo sviluppo di macchine compatte e quanto più
possibile integrate, al fine di ridurre i costi di installazione e manutenzione.
Bausano rinnova la serie Multidrive
In questi ultimi due anni Bausano ha intrapreso un programma di
rinnovamento della gamma di estrusori bivite Multidrive. I primi frutti di questo lavoro
sono visibili al Plast (Pad. 25 - Stand C 12 ): si tratta dei nuovi estrusori MD 52, MD 90
ed MD 170, destinati ad affiancarsi - ed in parte sostituire - i precedenti modelli MD.
Basati sul collaudato (e brevettato) schema di trasmissione a suddivisione della coppia
motrice Multidrive, i nuovi estrusori sono caratterizzati da un elevato rapporto L/D, che
arriva ad assumere valori compresi fra 1/25 e 1/30. Lallungamento dellunità
di plastificazione consente di ottenere una maggior resa anche con bassi regimi di
rotazione delle viti, a tutto vantaggio della durata delle camere di plastificazione;
maggiore lunghezza significa anche un tempo di permanenza ottimale del materiale ed una
capacità di scambio termico superiore, tale da permettere una migliore plastificazione
del polimero anche alle alte portate.
Il maggior sforzo è supportato da un riduttore a quattro assi, completamente ridisegnato,
provvisto di una nuova dentatura degli ingranaggi allo scopo di ottimizzare la
trasmissione di potenza. La potenza è sviluppata da motori asincroni con comando a
convertitore di frequenza, basati sul sistema DTC ( Direct Torque Control) che permette di
ottenere il massimo della coppia già a bassi regimi di rotazione.

Nella serie MD, la gestione degli estrusori è affidata ad una nuova generazione di quadri
comando (PCL) dotati di consolle pensile con schermo a colori, compatibili con una larga
fascia di PC e di programmi standard per semplificare lintegrazione con unità di
controllo periferiche. I nuovi quadri offrono un report completo dei parametri di lavoro
su stampante o su PC in remoto, in questultimo caso per il controllo di più
macchine oppure per le operazioni di teleassistenza a distanza (attraverso modem). I nuovi
estrusori possono essere equipaggiati anche con quadro pensile a strumentazione singola,
con termoregolatori dellultima generazione a doppia banda P.I.D. e logica di
autotuning, in grado di scegliere autonomamente i parametri più adatti al mantenimento
delle temperature impostate.
Completano il programma espositivo un nuovo banco profili con controllo a PLC e gli
estrusori monovite con gruppo calandratura Compact.
Presenza a tutto campo per il Gruppo Colines
Il Gruppo Colines opera sia nella progettazione e costruzione di macchine ed impianti,
sia nella trasformazione dei polimeri: questa doppia prospettiva si rivela preziosa, in
quanto permette di sviluppare sinergie e feed-back tra le diverse società del gruppo.
Di particolare interesse è la costruzione di impianti cast film per applicazioni quali
film a bolle, film per PP, film barriera fino a 5 strati e stretch film. Recentemente il
Gruppo Colines ha fornito ad un grosso gruppo petrolchimico un impianto combinato per la
produzione di CPP film e film per pannolini. In questo segmento, la società è anche in
grado di fornire impianti, con unità monostiro, per la produzione di film traspiranti
(breathable film). Lunità di monostiro, frutto della ricerca Colines, è una
macchina polivalente capace di orientare film monoestrusi o coestrusi da tre a cinque
strati, per impieghi diversi, tra cui pannolini, film estensibili e imballaggi alimentari.
Con alcuni lievi accorgimenti, la macchina può passare con la massima flessibilità tra
le diverse produzioni, caratteristica particolarmente apprezzata nei paesi in via di
sviluppo.
Nel segmento del film a bolle, il Gruppo Colines ha già venduto nel mondo un centinaio
di impianti. Anche in questo caso la flessibilità è tenuta in massimo conto allo scopo
di soddisfare le diverse esigenze di trasformazione: da impianti semplici a ridotta
produzione oraria fino ad linee avanzate capaci di elevate produttività. I livelli
prestazionali di queste linee sono stati incrementati negli ultimi anni, ed ora combinano
elevate velocità con alte produzioni, anche in presenza di basse grammature. Macchine
sempre più automatiche, dotate per esempio - di robot per il taglio e per
lincollaggio automatico del film in testa ed in coda. Gli impianti più recenti
presentano una capacità di estrusione fino a 1.200 kg/ora di film PE, larghezza utile
rifilata di 3.000 mm, peso minimo del film di 50 gr/m2. La velocità meccanica della linea
raggiunge i 110 m/min.
Il Gruppo Colines ha anche sviluppato tecnologie innovative. Partendo da un impianto per
film a bolle daria, il costruttore ha messo a punto una linea per la produzione, in
ununica fase, di una struttura composita costituita da una foglia sottile di
alluminio, un film a bolle daria e una seconda foglia di alluminio. Il multistrato
è destinato ad applicazioni in edilizia, per esempio plafonature, isolamento termico di
impianti per aria condizionata e rivestimenti decorativi.
Unaltra interessante tecnologia, brevettata, è Ondubol, con cui si ottiene una
lastra/foglia ondulata rigida o flessibile di polipropilene. I pannelli Ondubol sono
robusti, flessibili, leggeri, resistenti allacqua; sono quindi impiegati in diversi
settori, quali edilizia, agricoltura e imballaggio di prodotti alimentari, ma vi sono
altri ambiti applicativi ancora da sviluppare; per esempio, laccoppiamento delle
sottili lastre con alluminio per realizzare pannelleria isolante per il fondo dei
frigoriferi. Una variante di questa tecnologia riguarda i pannelli rigidi termoformati
Bubbleguard, composti da due strati esterni di PP che racchiudono allinterno una
struttura ondulata o a bolle. Questi pannelli monomaterici, estrusi in ununica fase
senza luso di adesivi, promettono interessanti applicazioni nellindustria dei
trasporti (componenti di carrozzeria), nellimballaggio industriale e
nelledilizia.
Retrofitting: un nuovo software risolve i problemi
Mitsubishi Electric e Resotec Realtime Software Technick hanno recentemente annunciato
un programma di collaborazione per lo sviluppo di controlli elettronici destinati al
settore delle materie plastiche. Al Plast (Pad. 20 Stand A09) viene presentato, in
anteprima per il mercato italiano, il primo frutto di questa collaborazione:
Extrusion-pack2, sistema di controllo sviluppato pensando anche allutilizzatore
finale che ha necessità di effettuare retrofitting di macchine esistenti. Extrusion Pack2
è già pronto ed ingegnerizzato; deve essere solo configurato per la linea di estrusione
intervenendo direttamente sullo schermo grafico del pannello operatore, senza il bisogno
di strumenti o software di programmazione specifico. Mitsubishi Electric e Resotec sono
anche in grado di fornire soluzioni complete preconfigurate che possono essere integrate
facilmente e velocemente nella macchina, offrendo così un elevato risparmio di tempo e
denaro.
Sebbene già pronto per soddisfare tutte le necessità di una normale linea di estrusione
dotata di vari accessori, Extrusion Pack2 si propone come sistema aperto alle specifiche
esigenze degli utilizzatori, che possono personalizzare il prodotto utilizzando un
pacchetto standard di programmazione software per PLC (Melsec Medoc +, conforme alla norma
IEC 1131) e un software di sviluippo per i pannelli operatore HMI (VISU4WINNERS).
Novità nella mescolazione in continuo
Divisione del gruppo Techint, Pomini ha raggiunto unelevata specializzazione
nella produzione di mescolatori continui e discontinui, estrusori monovite e bivite, oltre
a diverse tipologie di teste di granulazione. La tecnologia Pomini per la mescolazione
continua è ben rappresentata dal mescolatore continuo lungo LCM, disponibile anche con
scarico assiale (LCM-AX). Si tratta, in estrema sintesi, di un mescolatore controrotante
tangenziale doppio che alimenta un estrusore monovite per degasare, pompare e
pallettizzare il materiale, con tecnologia a doppio stadio. LCM AX è il modello bivite
corotante e compenetrante, con tecnologia a singolo stadio.
Pomini sta attualmente mettendo a punto un nuovo prodotto per la mescolazione in continuo,
denominato Techint Continuous Compounder (TCC), che combina i vantaggi della tecnologia
bistadio LCM con quelli che si ottengono impiegando una pompa ad ingranaggi per le fasi di
pompaggio, filtrazione e pellettizzazione. Confrontato con i tradizionali mescolatori a
due stadi, TCC potrebbe offrire una maggiore produttività e versatilità dimpiego,
ridotti consumi energetici e la possibilità di eseguire il degasaggio forzato. Rispetto
alle tecnologie tradizionali bivite, presenta inoltre una costruzione meccanica più
robusta e, al tempo stesso, semplificata. Entro il 2001 sarà disponibile la versione da
laboratorio TCC 100, equipaggiata con filtrazione continua e testa di taglio
sottacqua.
Linee Berstorff per gomma, masterbatches e compound
Tre estrusori spiccano nel programma espositivo della Berstorff al Plast 2000 (Pad. 9/1
- Stand D04 / E05): la serie ZE Ultra Torque per il compounding ad elevate prestazioni, la
serie Compex MPC per materiali particolarmente termosensibili e, nel settore gomma, la
nuova generazione di estrusori monoviti GE-Compact.
Gli estrusori bivite ZE Ultra Torque possiedono elementi di vite a stretto ingranamento.
Caratteristiche di questa serie sono portate e coppie elevate, nonché ottima dispersione
grazie agli alti gradienti di taglio. Le macchine sono indicate per il compounding di
termoplastici standard (PE, PP, PS), tecnopolimeri (SAN, ABS, PA, PC) e termoplastici
high-tech, quali PEEK, PPO, PSU.
Lestrusore esposto al Plast è il modello da laboratorio ZE 25 Ultra Torque, dotato
di un riduttore mobile (che agisce posteriormente) servito da un azionamento elettrico
separato. In questo modo le viti, anche se a contatto con il polimero, possono essere
rapidamente estratte (parzialmente o completamente) dal cilindro e reintrodotte con la
stessa facilità nella loro posizione di lavoro; il tutto senza la necessità di spostare
dosatori ed apparecchiature a valle. In ogni istante, quindi, si può controllare lo stato
della miscelazione, la colorazione o la fusione allinterno dellestrusore.
Gli estrusori Compex MPC sono invece rivolti alla miscelazione di additivi termosensibili,
oppure alla produzione di masterbatches colorati od altri compound speciali (per esempio
prodotti antifiamma), quando è richiesta una lavorazione a bassa degradazione termica.
In Fiera Berstorff espone il modello Compex MPC 48 che, in funzione del prodotto e del
processo, può raggiungere portate fino a 800 kg/h. Caratteristici di questi estrusori
sono gli elementi di vite non ingrananti MPC e gli elementi di ritegno. La combinazione di
questi due componenti permette di fondere i materiali in modo molto delicato ed uniforme,
senza punte di temperatura e con degradazione termica ridotta al minimo. Con la stessa
configurazione vite si può lavorare circa il 70 % dei polimeri, una soluzione che
accontenta gli operatori che richiedono unelevata flessibilità produttiva.
Infine, il costruttore tedesco presenta la nuova generazione di estrusori GE-Compact,
destinati alla produzione di semilavorati, in particolare profilati per lindustria
automobilistica e le costruzioni. Lestrusore esposto è munito di pompa ad
ingranaggi, configurazione particolarmente indicata per ottenere profilati con tolleranze
dimensionali molto contenute. Le centraline di termoregolazione e tutto limpianto
elettrico sono integrati nella struttura della macchina. Lestrusore, montato su una
piastra base, può quindi essere collegato e messo in esercizio rapidamente. Il controllo
avviene per mezzo di un PLC con monitor rotante; completa lequipaggiamento un motore
di azionamento trifase a regolazione di frequenza, oppure - su richiesta - un motore a
corrente continua.
Per diametri vite fino a 120 mm, lestrusore è provvisto di una zona con rullo di
alimentazione fisso per facilitare lintroduzione della gomma (su richiesta, il rullo
di alimentazione può essere incernierato); completano la dotazione unampia gamma di
accessori che permettono di trasformare la versione standard in una macchina ad alta
tecnologia, secondo le diverse esigenze del processo produttivo.
Estrusori e teste Tecnomatic
Ricco
programma espositivo anche per la società bergamasca Tecnomatic (Pad.25 Stand
C11). Si comincia dallestrusore monovite modello LC-1.75.30 per poliolefine e PVC
plastificato, ottimizzato per incrementare le prestazioni in termini di produttività e
capacità di plastificazione. Lintervento ha preso in considerazione anche il
miglioramento dellambiente di lavoro, attraverso la riduzione delle emissioni
sonore. Ulteriori vantaggi vengono dalla possibilità di scegliere tra motorizzazione in
corrente continua o in corrente alternata, che elimina numerosi interventi di manutenzione
e riduce i consumi energetici.
Gli estrusori Tecnomatic sono caratterizzati da una solida struttura di supporto in
acciaio, riduttore ad assi paralleli sovrapposti, cilindro e vite nitrurati, sistema di
riscaldamento e raffreddamento del cilindro con manicotti alettati che assicurano
unelevata capacità di raffreddamento anche nelle applicazioni più critiche.
Particolare attenzione è stata posta al sistema di controllo, che nella versione standard
impiega termoregolatori singoli più affidabili. Il sistema comprende la regolazione della
velocità di estrusione mediante azionamenti a velocità variabile, lindicazione dei
giri vite e dellassorbimento del motore; a richiesta è disponibile la
visualizzazione di temperatura e pressione del fuso sulla flangia di uscita
dellestrusore. E anche possibile raggruppare i comandi della linea su un
quadro pensile rotante o, sempre a richiesta, inserire un sistema centralizzato che
registra le ricette, visualizza in chiaro gli allarmi ed offre la duplicazione di tutti
gli strumenti di visualizzazione e controllo, fornendo una rappresentazione sinottica
della linea.
Presso lo stand Tecnomatic si può ammirare anche un coestrusore modello LC-1.30.24
completo di anello adattatore, particolarmente adatto per la coestrusione di strisce
colorate sui tubi. Il dispositivo, che lavora poliolefine e PVC, è equipaggiato con un
motore in corrente alternata - azionato da inverter, riduttore e reggispinta - ed è
montato su colonna e ruote pivottanti, quindi orientabile e regolabile in altezza. Il
coestrusore, completo di tramoggia in acciaio inossidabile, presenta un diametro vite di
30 mm e rapporto L/D pari a 1:24. E stato migliorato anche il gruppo di
plastificazione, con linserimento di serie di un inverter vettoriale. Tra
laltro, è ora disponibile un modello dotato di motore brushless, per sincronizzarsi
con l'estrusore principale.
Il programma espositivo prevede anche quattro teste di estrusione. Il modello LC-63V, a
raggiera, è rivolto allestrusione di tubi in PVC con diametro esterno da 315 a 630
mm; la testa è in acciaio al carbonio C-45, cromata ad alto spessore sulle superfici a
contatto con il polimero. La testa LC-40E, con distribuzione a volute, è invece indicata
per la produzione di tubi in PE da 180 a 400 mm. Completano la gamma una testa per bitubo
PE, con diametro 40/40 mm, e la nuova testa AD, ad alta distribuzione, particolarmente
innovativa. Questo modello, attualmente in fase di test presso un importante cliente,
presenta una distribuzione del materiale ottimizzata in modo da consentire, prima ancora
di montare le filiere, la produzione di tubo perfettamente formato. Offre, inoltre, un
miglioramento delle tolleranze dimensionali di diametro e spessore su tutta la
circonferenza, ridotta caduta di pressione, aumento di produttività. La testa AD è
indipendente dal tipo di polimero impiegato e richiede filiere più corte. Il progetto,
terminata la fase di test, sarà esteso a tutta la gamma di dimensioni.
Il Plast è anche loccasione per presentare la vasca di calibrazione VV250/6.1.2
per tubi con diametro esterno da da 50 a 250 mm. La struttura portante è in carpenteria
d'acciaio, mentre il corpo è realizzato in acciaio inossidabile. La vasca presenta una
zona di vuoto ed è predisposta per due stadi di calibrazione. Miglioramenti sono stati
apportati al circuito idraulico ed allimpiantistica, che ora utilizza tubazioni
rigide meno soggette a perdite. Il nuovo circuito del vuoto, inoltre, presenta una ridotta
rumorosità ed offre un migliorato controllo dimensionale. Infine, grazie ad uno speciale
cestello sono stati allungati gli intervalli di manutenzione dei filtri.
La coestrusione secondo Amut
Numerose, come sempre, le proposte della Amut, presente al Plast nel Pad. 9/1 - Stand
D14-F09. Il programma espositivo comprende, innanzi tutto, una nuova linea per la
produzione di profili finestra coestrusi, attraverso il rivestimento esterno del profilo
con polimero vergine, mentre il nucleo (pari al 70% del totale) è costituito da materiale
proveniente dal recupero su grande scala di vecchi infissi. La linea utilizza un estrusore
bivite parallelo della nuova serie 2000, modello BA 92, dotato dei nuovi riduttori Amut
con momento torcente migliorato (fino al 50% superiore rispetto ai precedenti modelli),
grazie a ai quali si arriva agevolmente a portate superiori a 350 kg/h. Lunità di
coestrusione, una bivite conica KBA 48, è stata progettata per essere abbinata alla
macchina principale in modo funzionale; in particolare, uno speciale supporto snodato -
parte integrante del basamento della macchina supporta il coestrusore, rendendolo
così basculante e facilmente collegabile al blocco di coestrusione. La linea può
raggiungere velocità d'estrusione fino a 5 metri al minuto, in funzione del peso lineare
del profilo.
Allo stand Amut viene esposta in funzione anche una linea completa per la
produzione di foglia coestrusa espansa di PP. Limpianto è equipaggiato con un
estrusore monovite (diametro 100 mm) caratterizzato da elevate prestazioni e flessibilità
desercizio, per venire incontro alle esigenze dei produttori di imballi
termoformati. In funzione del polimero impiegato si possono raggiungere portate da 350
kg/h (nel caso di PP espanso) fino ad oltre 500 kg/h (HIPS).
Per lestrusione di tubi sono annunciati due modelli: un estrusore BA 130 serie 2000
(L/D=26:1) per la produzione di tubi in PVC rigido con capacita di 1.300-1.400 kg/h e
relativa testa di estrusione da 400 mm; un estrusore monovite EA100 per tubi in HDPE,
equipaggiato con testa da 250mm e caratterizzato da capacità produttiva di 750 kg/h.
Per mostrare al pubblico le prestazioni dei nuovi impianti per tubi in HDPE, nei giorni
della Fiera è prevista anche una open-house presso il nuovo reparto R&D di Novara,
dove viene esibita in funzione una linea completa per lestrusione di tubo in HDPE
(PE 100). La linea, con estrusore da 75 mm, produce 500 kg/h di tubo con diametro 110 PN
6.
Infine, lo stand Amut ospita anche una speciale calandra orizzontale per estrusione di
foglia e lastra di PET con larghezza di 1.200 mm.
Estrusori bivite corotanti Maris
Maris presenta al Plast (Pad. 25 - Stand C16/D27) la serie di estrusori bivite
corotanti TM HT, frutto di anni di ricerca e sperimentazioni eseguite presso il centro di
prove e processi, e confermate in test con alcuni clienti.

Questa linea di macchine rappresenta a detta della società - la sintesi di
unevoluzione costante della progettazione e costruzione di estrusori, un binomio tra
meccanica avanzata e conoscenza del processo di compoundizzazione sviluppato all'interno
della Maris.
Cast film a tre strati
Nextrom presenterà le sue tecnologie di estrusione tubi e film al Plast (Pad.9/2
stand B04), ma gli impianti di maggiore dimensione saranno esposti presso lo
stabilimento di Cusano Milanino, a 20 minuti di bus dalla Fiera, collegato attraverso un
servizio navetta continuo. Lopen house è rivolta, in particolare, ad un impianto
cast film a tre strati e ad un avvolgitore automatico per tubi flessibili.
Limpianto cast, modello FCL21/SH, è in grado di produrre stretch film coestruso a
tre strati con larghezza utile di 2.000 mm, velocità meccanica pari a 600 m/min e
produzione netta di 900 kg/h. La linea comprende tre estrusori (160DEKC, 90 DEKC e 75
DEKC) con vite barriera ad alte prestazioni più un estrusore 90 R che alimenta,
direttamente nel cilindro principale, i rifili laterali e compattati provenienti dal
riciclo in linea. La testa piana è dotata di tasselli termici per il controllo dello
spessore e feed-block per la coestrusione dei tre strati. Presente sullimpianto
anche una lama aspirante a doppia camera, sviluppata da Nextrom per assicurare la perfetta
adesione del film alla superficie del chill-roll e conferire così al film elevate
caratteristiche ottiche e qualitative. Il gruppo chill-roll ha un rullo principale con
diametro di un metro; i canali di distribuzione dellacqua di raffreddamento sono
stati progettati per garantire uno scambio termico ottimale.
Completa la linea lavvolgitore BVA 2100, caratterizzato da un nuovo sistema di
avvolgimento e da sistemi di controllo della tensione e della pressione, con velocità
massima di 500 m/min. Lavvolgitore comprende anche un robot per lo scarico
automatico delle bobine ed il riposizionamento dei mandrini nel magazzino della macchina.
Lintera linea sfrutta gli ultimi sviluppi Nextrom, quali controlli di velocità con
nuovi servomotori brushless e trasduttori per il controllo dei tiri.
Tra le novità, segnaliamo anche il bobinatore automatico MWB 1300P, destinato a tubi
flessibili e semi-rigidi con diametro esterno fino a 32 mm; la macchina è in grado di
operare con bobine di diametro fino a 1.300 mm e velocità massima di 60 m/min. Un
dispositivo, anchesso di nuova concezione, consente di regolare il diametro interno
della bobina da 390 a 980 mm.
Infine, Nextrom presenterà in occasione del Plast anche gli ultimi sviluppi relativi ad
impianti per film soffiato in bolla, nonché recenti innovazioni nellestrusione di
tubi compositi e tubi con silano
Doppia esposizione per Plastimac
Plastimac è presente in Fiera in due diverse aree espositive, una dedicata
allestrusione-soffiaggio di corpi cavi (Pad.20-B13/A18), laltra alla
produzione di film (Pad.12 - A08/B11/B13). Inoltre, presso lo stabilimento di Corsico è
stato allestito uno show room dove vengono mostrate in funzione altre soffiatrici della
gamma Plastiblow.
Nel campo dell'estrusione-soffiaggio la società milanese espone due nuove soffiatrici
Plastiblow. La prima è la PB4000/D, una macchina in grado di produrre contenitori con
volume fino a 5 litri; questo modello si caratterizza per il movimento in piano dei gruppi
portastampi su guide lineari a ricircolo di rulli. Tale soluzione, che risulta ottimale
per le produzioni multicavità, aumenta l'affidabilità della macchina e riduce al minimo
gli attriti, riducendo i costi di produzione.
L'accessibilità agli stampi e la semplicità delle regolazioni sono altre caratteristiche
molto apprezzate dagli operatori, in particolare da coloro che richiedono rapidi cambi di
produzione. Per migliorare la sicurezza della macchina, oltre alle classiche protezioni e
segnalazioni di pericolo, sono stati introdotti diversi controlli, tra cui un sistema
brevettato che consente la regolazione assiale dell'ugello di soffiaggio anche a cancello
chiuso.
La soffiatrice PB4000/D presenta una corsa allungata dei gruppi portastampi e monta una
testa tripla per la produzione di flaconi HDPE/PP da un litro per concimi liquidi, con una
cadenza di circa 1.800 pezzi/ora. La macchina esposta in Fiera è anche dotata di un
dispositivo, integrato nel pannello di comando, per il controllo di qualità dei flaconi.
Una linea di recupero trasporta il materiale verso un granulatore; il macinato così
ottenuto è reinserito in ciclo dopo miscelazione con materiale vergine e master.
La seconda soffiatrice esposta a Milano è una PB500/D destinata alla produzione di
flaconi in PET (fino a 500 cc) per impieghi farmaceutici. Equipaggiata con un estrusore da
50 mm di diametro azionato da motore asincrono ed inverter, la soffiatrice è dotata di un
sistema di controllo Moog con display TFT ad alta risoluzione basato su standard PC e
sistema operativo Windows NT. Il sistema consente di controllare gli spessori del parison
impostando in modo intuitivo un profilo con un massimo di 400 punti. L'interfaccia, basata
su PC, consente anche una veloce trasmissione di dati in caso di teleassistenza via modem
o di collegamento di diverse macchine in rete.
Nel Padiglione 12, Plastimac espone tre termosaldatrici automatiche: DB100E SH e DB80G SH
per la produzione di sacchetti con maniglia soffice, rispettivamente con soffietto di
fondo o soffietti laterali, ed il modello DB106E BLOCK per la produzione di buste a bocca
aperta con e senza "block". In mostra anche due linee di estrusione film in
bolla: MB35/700 per monostrato di polietilene e EXK65-50-50/1700 per la coestrusione a tre
strati di poliolefine.
Monobloc MB35/700 è un impianto di fascia stretta, per film di polietilene di larghezza
utile fino a 650 mm. La linea è dotata di un estrusore ad alimentazione tradizionale, con
vite in acciaio nitrurato del diametro di 35 mm e rapporto L/D 1:30. Il cambiafiltro è
del tipo a cartuccia, mentre la testa di estrusione è rotante, ad alimentazione centrale,
con possibilità di montare filiere da 60 a 100 mm di diametro. L'impianto dispone di sei
zone di riscaldamento (per l'estrusore, il cambiafiltro e la testa) con resistenze a
fascia in ceramica, ognuna controllata mediante termoregolatori digitali indipendenti.
L'anello di raffreddamento, ridisegnato per ottimizzare il flusso d'aria, é provvisto di
un ventilatore insonorizzato e monta inserti regolabili, studiati appositamente per la
lavorazione del polietilene.
La seconda linea, EXK50-65-50/1700, è rivolta alla coestrusione a tre strati di film
tecnici (LDPE, LLDPE, mLLDPE, HDPE, MDPE, mMDPE, PP, EVA, DuPont Surlyn), con capacità
produttiva di oltre 300 kg/h. Limpianto comprende due estrusori da 50 mm ed uno da
65 mm, tutti con vite barriera (L/D 1:30) e sistema ad alimentazione forzata del granulo.
La testa di coestrusione a tre strati, fissa e dotata di filiera cromata da 250 mm, monta
un distributore a spirale progettato per eliminare eventuali differenze di velocità di
flusso del melt (dovute al gradiente di temperatura) nei canali interni; si ottiene così
un sensibile miglioramento delle proprietà ottiche e meccaniche del film, oltre ad una
maggiore uniformità degli spessori. L'anello di raffreddamento in lega di alluminio é
stato modificato per ottimizzare il flusso d'aria.
La regolazione della portata d'aria del ventilatore é ottenuta mediante un variatore di
frequenza digitale (inverter). La bolla è anche raffreddata allinterno mediante IBC
(Internal Bubble Cooling). Il banco di stiro oscillante (a 360°), a barre orizzontali, è
dotato di inverter per il controllo della velocità di rotazione; ciò consente di
distribuire su tutta la circonferenza del tubolare le eventuali disomogeneità di spessore
che si generano durante il raffreddamento della bolla, e di conseguenza il rischio di
ottenere bobine "coniche".
L'avvolgitore, a doppia stazione, é totalmente automatico. Completano l'impianto un
allineatore digitale, indispensabile per lavorare con punte oscillanti, ed un avanzato
sistema gravimetrico multistadio capace di pilotare autonomamente l'intera linea di
coestrusione.
Linea per la produzione di foglia PP
Union mostra in Fiera (Pad. 25 - stand C10) un impianto per foglia di PP, con
produzione oraria di 800 kg/h e larghezza dei cilindri pari a 1.200 mm. Limpianto è
composto da un estrusore monovite TR 160, cambiafiltro senza interruzione di flusso, pompa
ad ingranaggi UGP 370, testa piana, calandra tipo FI 3X600X1200 e quadro comando con PLC.
Limpianto FI con calandra inclinata è il più avanzato prodotto da Union. La
calandra, in grado di produrre ogni tipo di foglia per termoformatura PP (da 200 a 2000
micron), è azionata da tre motori indipendenti sincronizzati; la chiusura dei cilindri è
meccanica con pressione lineare fino a 120 kg/cm. Da segnalare la presenza di un
dispositivo per il disassamento del cilindro centrale (cross-axis), utile per calandrare
foglia con spessore di 200 micron. Unaltra caratteristica è la facilità di
passaggio dal sistema calandra al sistema cast con lama daria. Infine, il sistema di
entrata del materiale consente di costruire la testa con uninclinazione particolare,
che facilita tra laltro - lintervento delloperatore per la
regolazione degli spessori.
|